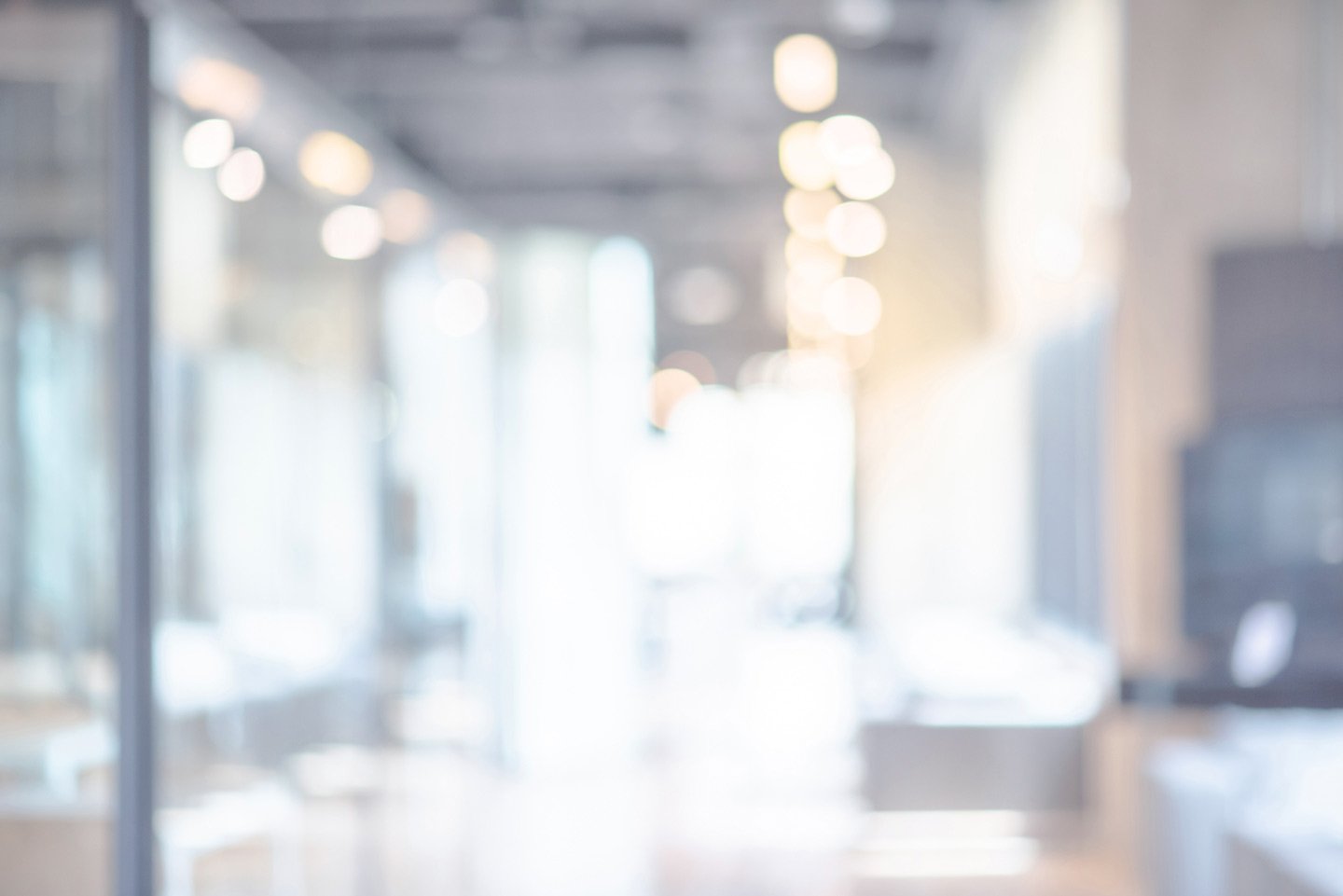
While chief operating officers and compliance leaders acknowledge the importance of having a business continuity plan (BCP), many organizations remain unprepared for emergencies that can and do happen. If there is a plan, it’s often focused on IT recovery, overlooking other critical assets, such as people.
There’s a myth that planning for the unknown is difficult, with too many moving parts and “what-ifs.” This type of planning doesn’t have a natural home in many organizations, so nobody is on point to champion the cause. Yet without it, companies find it tough and costly to recover from the unexpected.
Business continuity planning is a hot topic for organizations across the country due to the recent increase in natural disasters such as fires, floods, severe storms, and the concerns about a mega-earthquake on the West Coast. Security concerns are also higher than ever due to the litany of massive data breaches and growing concerns about terrorism.
Given the importance of disaster planning to healthcare organizations, who are typically on the front line during emergencies, FamilyCare Health, a Portland-based Coordinated Care Organization, recently completed its own business continuity plan to enhance preparedness for a natural disaster. Here are the steps they took.
Without some forethought, true priorities may be unclear in the face of a disaster, when resources are strained. The cascading effect of events demands that your organization knows what to address first. FamilyCare Health created department-specific business impact assessments identifying key people, processes, and technologies.
Additionally, they highlighted key company-wide processes in need of protection and worked with the executive team to gain alignment across the organization. With priorities clear and stakeholders on board, FamilyCare Health next considered the following:
- Critical business functions and people
- Critical SLAs and cadences (such as payroll)
- Critical external partners, such as vendors and government agencies
- Internal interdependencies (such as Finance and HR)
- How a disruption would impact each line of work
- How long a group could operate without a key process before irreversible damages would occur
- Past disruptions and what has been tried before
- Any upcoming changes worth noting
- A wish list of ideas for adding resilience
Once critical business processes and recovery plans were created, FamilyCare built a nimble, action-oriented plan that addresses key vulnerabilities and provides practical solutions.
The organization conducted small-group interviews with teams like IT or HR to start the planning, during which participants walk through what they would do in case of an emergency.
The process of planning is itself the critical piece. It promotes communication among your teams and empowers them to make changes.
Next, FamilyCare documented lessons learned and ideas for improvement and captured these lessons learned to create a final plan.
To test its plan, FamilyCare conducted a customized three-hour simulation designed to “stress-test” the BCP. During the simulation, FamilyCare walked through what they would do in case of an emergency and identified gaps and opportunities for improvement.
As FamilyCare discovered, it’s critical to emphasize the importance of personal readiness among your team. It’s analogous to the airline rule about putting on your own oxygen mask before you help someone else. If employees worry about their families and loved ones, they understandably won’t think about work.
Preparing for an emergency can seem daunting, and no amount of planning can prepare you for every situation.
However, the process of planning is itself the critical piece. It promotes communication among your teams and empowers them to make changes. It gives them a process for thinking through a potential crisis and learning firsthand from a simulated experience.
You’ll have a systematic way to plan that will leave you far ahead of where you’d have been without it. Your company, your brand, and your customer relationships will all be the better for it.
This article was originally published in the Portland Business Journal. Check it out here.
RELATED INDUSTRIES
RELATED SOLUTIONS