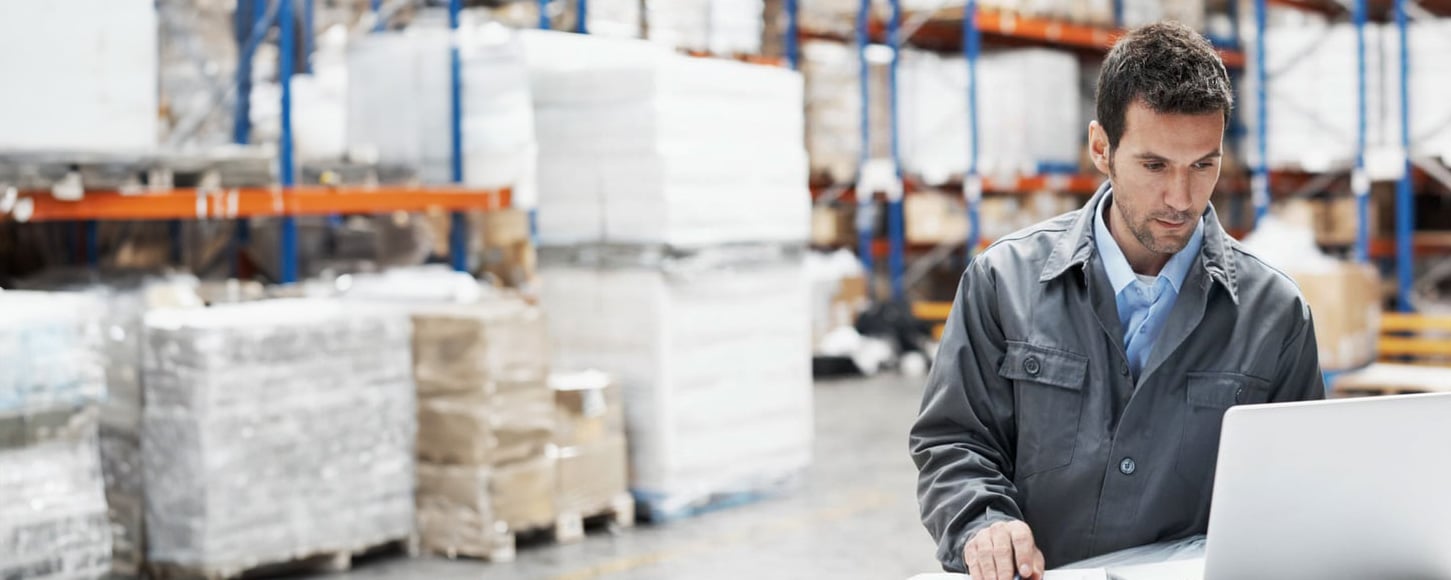
Challenge
One of the world's largest retailers was ready to take a close look at its global supply chain. Over the years, layers of new and increasingly complex products, services, packaged goods, locations, channels, suppliers and distributors grew with the business, causing cost structures and performance to become more opaque. It was clear that a bloated supply chain was slowing delivery times and duplicating efforts, so they engaged Point B to partner with its Global Strategy team to assess its supply chain. Based on the outcomes of that assessment, they asked us to lead them through a Lean transformation.
Reasons to Believe
Our client was no stranger to Lean principles, but past efforts had fallen short. Building clarity, confidence and buy-in throughout the organization early on would be critical to success.
We collaborated with internal supply chain teams to survey more than 350 stakeholders and conduct 15 employee insight workshops. Together we identified six key focus areas: Metrics; Forecasting & Planning; Technology; Sourcing; Continuous Improvement/Lean; and PMO/Governance. We began building an organization-wide capability for change in these areas by developing a one-page cohesive strategy.
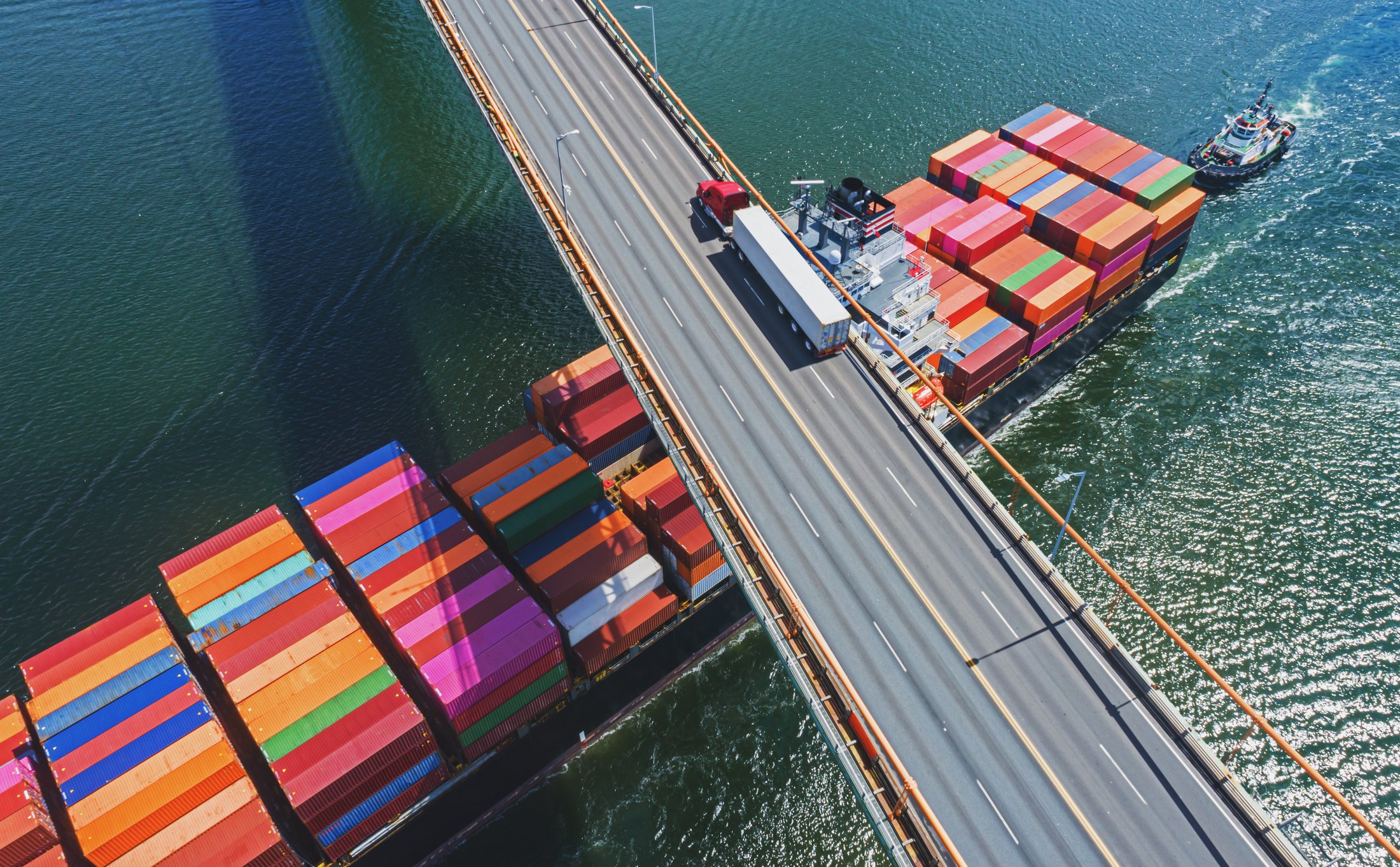
Through a number of sessions, we led stakeholder groups to a common understanding of the organization’s vision, goals, success measures and actions, focusing on the impact to front-line employees, managers and executive leaders.
With the right strategy and governance model in place, we built a 12-month continuous improvement roadmap based on Point B's ACT Framework™ (Accountability, Culture and Tools). We are now executing on that roadmap, which details the capabilities and activities needed to achieve our one-page strategy.
The leadership now enjoys improved communication and the company is already enjoying a groundswell of process improvements driven by front-line employees to identify waste and focus on activities that drive the greatest value.
Swift and Long-Term Wins
Within six months, a new manufacturing strategy was at work at a pilot plant. Operational efficiency improved by 57 percent and inventory accuracy increased from 55 to over 98 percent.
Most importantly, employees at all levels are now motivated by their Lean knowledge which empowers them to increase customer value and contribute to the organization’s strategic priorities.
Operational efficiency improved by 57 percent and inventory accuracy increased from 55 to over 98 percent.
RELATED INDUSTRIES
RELATED SOLUTIONS